Metodologia na avaliação de integridade estrutural
- Kleber Medina
- 19 de jul. de 2022
- 5 min de leitura
A metodologia de avaliação de integridade estrutural se divide basicamente em 3 etapas:
- Planejamento;
- Inspeção;
- Análise de Resultados.
Planejamento
A técnica a ser adotada para inspecionar os elementos de interesse de uma planta, equipamento ou processo depende de fatores específicos que variam muito de um projeto para outro, porém basicamente é válido selecionar pontos onde, ora por características do processo, ora por influência do ambiente externo, apresentam ser mais suscetíveis à defeitos ou desgastes. Desta forma, a seleção dos componentes mais críticos para inspeção pode ser feita com base:
- Nas condições operacionais: componentes que operam com maiores pressões, temperatura e ambiente corrosivo;
- No histórico de operação do componente: componentes que apresentaram falhas na unidade inspecionada ou que em unidades similares em projetos passados, apresentaram características similares;
- No acesso do componente;
- Nos riscos envolvidos no caso de falha do componente.
Nesta etapa é fundamental um cuidadoso levantamento dos dados operacionais dos componentes, bem como dos relatórios de inspeções ou falhas anteriores. Na etapa de planejamento há também que se selecionar os ensaios que serão realizados no componente. Esta seleção é feita com base nos mecanismos de falhas passíveis de ocorrerem no componente em função de suas condições operacionais e ambientais específicas.
O grau de abrangência de um estudo de avaliação de integridade leva em conta os seguintes pontos:
- Nível de documentação técnica do equipamento ou estrutura disponível;
- Custo de reposição do equipamento ou estrutura;
- Custo e o risco de acidentes;
- Custo de manutenção extemporânea ou prolongada;
- Custo do lucro cessante e da sua reação em cadeia.
Por esta razão, na avaliação de integridade estrutural, a etapa de planejamento é a mais importante e a que mais exige conhecimentos por parte do inspetor.
Quantidades exageradas de ensaios implicam maiores custos de inspeção. Por outro lado, a seleção equivocada dos ensaios ou em quantidade aquém do necessário, põe em risco a validade do laudo de integridade do componente.

Inspeção
Na etapa de inspeção, são realizados em campo os ensaios não destrutivos especificados na etapa de planejamento ou a coleta de amostras para ensaios laboratoriais, quando for o caso. Para cada ensaio não destrutivo deve ser elaborado um relatório contendo condições de ensaio, componente e local da inspeção, os resultados do ensaio e laudo, com a assinatura do profissional executor.
Estes relatórios servem de base para a análise final dos resultados e o parecer sobre a integridade de cada componente avaliado.

Análise dos resultados
Nesta etapa, a vida remanescente dos componentes é calculada com base em modelos matemáticos que na maioria das vezes são alimentados por dados obtidos nos sistemas de monitoramento da unidade. Os resultados são confrontados com as estimativas realizadas com base nos ensaios não destrutivos executados na etapa de inspeção e desta análise são estabelecidas medidas a serem tomadas para garantir a integridade de cada componente que compõe a planta avaliada e o período máximo para uma nova inspeção.
Em 1986, o EPRI (Electric Power Research Institute) propôs uma metodologia para avaliação de integridade estrutural dos componentes por etapas, divididas em 3 níveis. Estas avaliações são progressivas, ou seja, o nível subsequente só é realizado quando esgotados todos os recursos do item anterior sem que seja possível um laudo seguro sobre a integridade do componente. Assim, inicia-se a avaliação no nível 1, passando-se para os níveis 2 e 3 somente se necessário.
O nível 1 ou avaliação preliminar baseia-se apenas no levantamento de informações, ou seja, nenhum ensaio é realizado. Nesta etapa, examina-se o projeto ou os parâmetros de serviços gerais para verificar se, com base em considerações mais conservadoras, o componente terá uma vida útil remanescente maior do que a prevista. É possível executar essa avaliação sem referências a medidas específicas da planta, desde que os parâmetros operacionais não excedam os de projeto. Entretanto, é normal, mesmo neste estágio, considerar os resultados de monitorações específicas de cada componente, o que deve ser realizado com cuidado, uma vez que a instrumentação que monitora condições de danos pode não identificar regiões em que condições extremas estão presentes. Porém, considerando a experiência industrial, é usualmente possível garantir que os dados usados nesse caso são conservadores.
O nível 1 não gera informações novas para o componente. Por esta razão, esta etapa é mais rápida e econômica. As informações utilizadas como base são:
- Informações de projeto: códigos e normas, ensaios e testes, desenhos, especificações de materiais, tratamentos térmicos, memórias de cálculo, fluxogramas de processo;
- Informação de fabricação: conformação de materiais, dimensões, relatórios de inspeção;
- Informações originárias de plantas similares: acidentes ou falhas ocorridas em plantas com projetos similares;
- Informação de operação: históricos de temperatura e pressão, paradas e partidas, registros de anormalidades, defeitos e seu acompanhamento, procedimento de operação, acidentes, planos de paradas, manutenções ocorridas, planos de inspeções;
Já o nível 2 exige a geração de novas informações sobre os componentes, através de:
- Inspeção por ensaios não destrutivos;
- Análise de tensões simples;
- Análise dimensional.
A análise de nível 3, também denominada análise complementar, é uma etapa bem mais cara, que só deve ser utilizada se as etapas anteriores não fornecerem informações suficientes sobre a integridade dos componentes. Esta etapa envolve programas computacionais e análises complexas como:
- Análise por elementos finitos;
- Avaliação da temperatura do tubo em função da espessura de camada de óxidos;
- Exemplo da vida remanescente de fluência.
A avaliação nível 3 baseia-se no conhecimento muito detalhado das condições de operação e propriedades específicas dos materiais. Assim, procedimentos sofisticados de instrumentação e análise são necessários para documentar as condições de operação local. No entanto, a experiência sugere que, mesmo com um conhecimento preciso de tensão e dos parâmetros de temperatura, a dispersão nas propriedades do material padrão irá introduzir incertezas nas estimativas de vida. Métodos de análise probabilística foram introduzidos para reduzir o conservadorismo da avaliação com base nas piores propriedades possíveis. Estes métodos são, no entanto, limitados, porque muitos dos aços utilizados em tubulação industrial são suscetíveis a mudanças nas propriedades do material com o tempo.
Assim, mesmo com os materiais disponíveis antes da operação, as mudanças nas propriedades como resultado da operação só podem ser estabelecidas por meio de ensaios pós-exposição. O tipo de ensaio necessário irá variar com o tipo de componente. Assim, por exemplo, se o componente está em risco de falha por fluência, os ensaios são realizados para avaliar a tensão de deformação e ductilidade. Por outro lado, avaliações de defeito são geralmente baseados em tenacidade do material, portanto o teste deve estabelecer tenacidade à fratura. Em geral, as avaliações serão frequentemente limitadas pela capacidade de se caracterizar com precisão a natureza e a extensão de defeitos presentes e a incerteza quanto às propriedades do componente. Estas limitações são muito reduzidas quando se pode remover amostras para análise em laboratório.
Além disso, a avaliação nível 3 é passível de aplicação de programas computacionais com sistemas bem sucedidos, já disponíveis, que são capazes de armazenar de informações relevantes sobre a planta de uma maneira lógica e permitir a classificação e recuperação destes dados, de modo que a análise necessária possa ser realizada com precisão e eficiência.
A abordagem tomada em cada um dos níveis é apresentada na tabela abaixo:
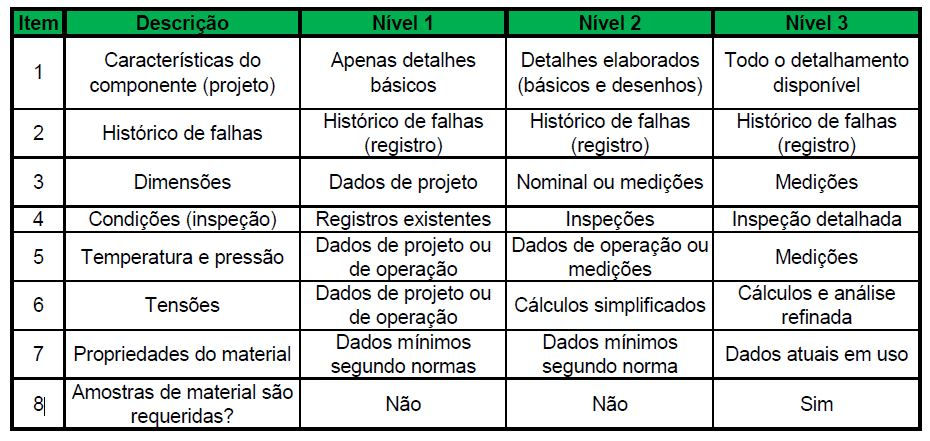
A conclusão de uma avaliação de integridade estrutural deve conter:
- Uma estimativa da vida residual da estrutura, caso as características operacionais continuem como até o presente momento;
- Programas futuros de inspeção e monitoração do equipamento;
- As ações necessárias para a aplicação de um programa de extensão de vida residual, tais como:
o Recuperação;
o Reforço;
o Repotencialização;
o Substituição de partes.
Fontes:
1. Arquivo pessoal;
2. Avaliação de integridade e estimativa de vida útil de componentes de caldeiras em UTES - Grupo de trabalho de manutenção de usinas térmicas - GTMT/ABRAGE - Belo Horizonte, publicado em 23 de Maio de 2013.
Comentarios